Job Description:
This position provides the functional strategy for the Division’s Global Supply Chain to ensure it has the capabilities and business architecture to meet the needs of the Division as well as guide the daily execution, performance improvement and career development of the Planning, Distribution and Transportation departments and their staff.

Key Responsibilities
Ensure delivery of all safety, customer service, quality, productivity, inventory and other financial metrics.
Accurately project and manage all costs including warehousing, freight, inventory and expired and obsolete inventory.
Ensure tight integration between Planning and Logistics and other Operations areas to optimize performance in schedule attainment, adherence and on time delivery.
Lead the implementation, ongoing management and effectiveness of the SIOP program.
Provide leadership to ensure accurate and timely input into the AOP and forecasting process as it pertains to inventory, expiry plans and cost projections.
Work with Site & Operations Directors to ensure capacity and capability expansion plans are timely, cost effective and operationally effective.
Create the Supply Chain Operations Strategic plan.
Manage the distribution objectives to ensure high quality, low cost and on-time delivery.
Manage staffing levels, IT solutions and outsourcing to support customer requirements while maintaining efficient operations
Manage the demand planning, supply planning and distribution requirements planning processes to ensure all service level and financial metrics are achieved.
Collaborate with Manufacturing, Quality Assurance, Sales, Purchasing and Customer Service to plan and route shipments in an efficient, cost effective manner
Respond to internal customer feedback through the use of continuous improvement strategies.
Participate in Divisional, Regional, or Corporate Operations councils or forums to drive best practice sharing.
Establish and implement regional supply chain strategies to support evolving business requirements and global supply chain strategies in partnership with divisional, regional and external stakeholders.
Guide Information System’s strategy and development for Supply Chain Operations, including Warehouse Management Systems (WMS), Enterprise Resource Planning (ERP). Forecasting and Transportation Management.
Ensure both owned and 3PL distribution warehouses are sized, designed and staffed properly, in line with future requirements spanning volume, handing, storage, shipping and value-added service.
Require routine, disciplined operational reviews that cascade through the organization to all levels enabling rapid escalation of issues for resolution and improved performance.
Apply the Global Trade Compliance Policy across the Division through direct or dotted-line reporting relationships with Site Leaders responsible for assuring development and implementation of procedures to ensure compliance with applicable global trade laws.
Ensure seamless integration of new products into the base replenishment process.
Ensure a safe work environment, working closely with HSE
Manage the department expense budgets and financial performance.
Provide for the continuous procedural improvement and staff adherence in order to comply with all GMP/QSR, and ISO requirements related to area of responsibility. Comply with all FDA, ISO, DOT and other regulations as communicated by Quality Assurance and Regulatory Affairs.
Evaluate spend and operating performance of our intercompany and finished goods outbound transportation lanes on a regular basis to assure performance is achieving stated goals and control thresholds.
Implement strategic programs to address evolving business requirements or issues, collaborating with our divisions, regions, carriers, freight forwarders, the Thermo Transportation Group (TTG) and other supply chain partners.
Participate in periodic bidding processes to re-quote the contracts with our carriers and other external transportation service providers, to achieve annual cost reduction targets.
This global role will align planning strategies across the Americas, EU and AP, lead the Global Planning function to improve core planning processes that result in improved product availability, reduced inventory turns, lower cost and lower scrap.
Minimum Requirements/Qualifications
Candidate will need to have strong analytic and data skills, strong people and influencing skills and leadership capability. The role operates in a complex, global matrix and involves driving the agenda across multiple functional groups and levels. Presentation and excellent verbal communication skills will be essential to allow for facilitation and report-out capability to Senior Management
Bachelor’s degree in business, manufacturing, logistics or related field. Advanced degree such as MBA or Masters in Supply Chain Management is preferred.
Extensive management experience in a multi-faceted Manufacturing and Distribution high volume, high mix, consumables and large equipment environment.
Demonstrated ability to increase operational throughput in a mixed model environment
Exposure to international distribution, including packaging labeling, export documentation, duties, regulatory approvals.
Broad knowledge of P&L, Balance Sheet, NPV/ROI, and foreign exchange is preferred.
Demonstrated experience and success using Lean business practices
Hands on experience using and specifying planning, DRP, inventory controls, replenishment, and warehouse management in ERP and best-of-breed software solutions is strongly preferred, with specific emphasis on SAP.
Experience in employee involvement principles, business and budget planning, execution, productivity and quality improvement methods.
Solid understanding of warehouse management software solutions.
Experience with Lean implementations.
Experience with project management concepts, needs assessment and cost modeling.
Experience in the optimal design and layout of a warehouse.
Willingness to travel 25-50% of the time
Desired Requirements
Knowledge of SPC, JIT, TQM, TPM, and TQC.
Knowledge of Six Sigma and Lean techniques /concepts.
Membership of CSCMP and/or WERC.
APICS certification.
Familiarity with medical device manufacturing preferred, but not required.
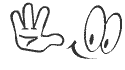