Quality Manager is a key member of the Doncaster leadership team and in addition to responsibility for quality assurance programmes and activities, plays an active role in the development and deployment of the mains lighting business strategy.
Watch: Career Advice

Lead the Quality Assurance function in the delivery of Quality Assurance programs across the site and promote growth by enhancing the reputation of the business through exceptional quality standards
Lead the organisation, planning, implementation, and control of a quality assurance program at the plant level and beyond which will reduce overall manufacturing costs
Lead the Quality function in the promotion of engineering principles and techniques. It will be responsible for driving these through all manufacturing and product support areas of the business in line with procedures, regulatory requirements and quality management objectives
Develop and implement quality management strategy plans, including resources, systems, time scales and financials to support, contribute to and integrate within Doncaster Lighting annual business plan and long term strategy
Deliver an effective communications strategy for improvement and awareness of quality issues across all departments
Lead the maintenance and continuous improvement of the plant and all internal Quality Management processes. Ensure the continued effective implementation of foundational quality systems such as Management Review, Internal Audit, Process Control, Corrective and Preventive Action as the management and voice of the customer representative
Lead a cross functional team of internal auditors
Lead Quality cost reduction activities within the business. Define and implement regular processes aiming for continuous improvement
Active participation in supplier selection process in coordination with sourcing department
Develop and maintain systems to monitor and improve supplier quality
Participate in engineering design reviews to ensure that new or modified products are manufacturable, repeatable and reliable
Act as champion for the Company’s Advance Product Quality Planning (APQP) and PPAP (Production Part Approval Process) processes in coordination with PROLaunch leader and sourcing Group
Lead the implementation of Divisional initiatives including reporting and communication requirements
Responsible for maintenance of closed loop corrective action (8D) for identified material nonconformance (i.e. supplier, in-process, Defect Escape, Customer Concerns)
Interface directly with customers and suppliers with regards to after sales service plus pre-order warranty terms contract negotiations and risk management
Provide a key interface to the various country sales organisations, including training and guidance for defect free specification plus support with concern management
Qualifications:
Engineering Degree or equivalent
Strong leadership experience
Quality Management experience within manufacturing type of company
Experience in keeping good relationships with customers and suppliers
CI, Lean Manufacturing, Six Sigma methodology experience, Six Sigma Black Belt would be an asset
Project Management Experience
Computer Literate (MS Office/Project/Visio, Minitab)
ERP Systems experience
Strong analytical skills
Problem Solving concepts (8D, A3, Root Cause Analysis etc.)
ISO9001/ISO Standards knowledge as well as auditing knowledge
Ability to work with all levels of the business
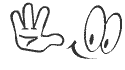
Send To A Friend